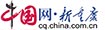
长安将“甲方”“乙方”绑在同一“战车”上
重庆长安汽车股份有限公司
拥有159年历史底蕴、37年造车积累,全球有14个生产基地、33个整车、发动机及变速器工厂。2020年,长安系中国品牌用户累计突破1900万,领跑中国品牌汽车。
近日,各大车企2月销量数据出炉,长安汽车继续稳坐“自主一哥”交椅,市场占有率再增1.5个百分点。业界人士认为:这与长安汽车的产业链供应链高效协同不无关系。
长安究竟做了什么?3月9日,重庆日报记者来到长安汽车全球研发中心一探究竟。
刚进门,记者立即发现一个奇怪的现象——这里有一群特殊的人,他们穿着各色工作服,与身着白色工作服的长安汽车员工泾渭分明。但他们又与长安的员工一起,忙碌在各个研发部门的岗位上,密切交流、不分彼此。他们,是长安配套企业的工作人员。
研发部门,是企业的“核心要地”,非长安本企业人员为何能深入这里?
长安—青山联合创新中心项目总监王海兵,是长安汽车全球研发中心“特殊人群”的一员。他介绍,目前,长安和青山正在就混合动力汽车的智能驱动进行联合攻关:青山工业派出机械、液压、软件、电机工程师团队“驻扎”在长安汽车,共同完成产品策划、定义、论证,并在长安汽车现场进行产品设计;到了样机试制、工程化开发阶段,长安汽车则会派出相应的技术团队常驻青山工业。
在这种联合开发模式下,青山工业在核心部件,以及长安汽车在动力总成匹配上的优势都得到充分发挥,开发速度是“各自为政”的两倍以上。
事实上,长安汽车与许多配套商之间,都已从过去供应链上的“甲方”“乙方”,演变成为利益共同体。高效协同研发,是这个利益共同体的关键特征。
重庆八菱汽车配件公司,是长安汽车的前脸格栅供应商之一。近期,在长安一款最新车型立项前,长安汽车突然召集八菱的技术人员到研发中心。一同被召集来的,还有数十家其他配套商。
长安汽车向各家合作伙伴抛出了关于新车型的想法:新车型必须要有众多的独创性设计和亮点。其中新车前脸的无边界格栅设计,就需要和八菱来共同实现。
长安汽车采购中心副总经理陈津介绍,传统的汽车开发流程,一般是由整车企业先出设计方案,再根据方案进行采购,如果发现供应商有不符合或达不到要求的零部件,就要进行设计层面的更改。几个来回,周期就会变长,也会产生额外的试错和沟通成本。
而现在,在新车型立项前就邀请主要供应商提前介入,把最优的设计,以及最优的成本、技术、交付的路线都确定好,这样可降低成本10%、单款车型开发周期缩短两个月以上,且产品的质量一致性和设计理念的实现度都会更好。
和长安“绑”在一辆“战车”上的“乙方”越来越多,且早已不限于汽车制造领域。
刚刚开启预售的长安高端车型UNI-K,搭载了腾讯和长安合作研发的汽车智能系统,该系统可以与人展开语音对话,响应收发微信消息等请求,同时能和手机实现跨屏联动。
据腾讯智慧出行战略设计总经理沈沛透露,早在2018年7月,腾讯和长安就合资成立了北京梧桐车联科技有限责任公司。腾讯利用自身在人工智能、大数据、云计算等领域的专业能力,为长安汽车赋能。由腾讯、长安等多家单位联合打造的智能超算中心,也布局在长安汽车公司内。
近年来,随着重庆汽车产业链向高端化、智能化延伸,大型互联网企业与重庆车企的合作风生水起。除了腾讯外,阿里巴巴也正与长安福特共建汽车行业工业互联网平台,通过大数据、智能化、云计算方式促进长安福特全生态链上万家企业降本增效;百度则在永川建设西部自动驾驶开放测试与示范运营基地,为车企智能化产品提供测试场地、链接自动驾驶领域相关资源。还有华为、科大讯飞……知名科技公司“跨界”赋能,让重庆汽车产业越来越有智慧。
“失真订单”为何在青山工业不见了?
重庆青山工业有限责任公司
中国兵器装备集团公司所属的国有大型工业企业,始建于1965年,资产总额逾36亿元,品牌价值逾40亿元。中国民族变速器行业领先者,DCT(双离合变速箱)在自主品牌中排名前三,现有配套企业100余家。
长期以来,制造业生产链供应链上的企业,都面临一个共同痛点:销售订单“失真”。
什么意思?简单而言,销售部门将订单传达给生产部门时,为了应对市场需求变化等不可预计的情况,需要保证一定的冗余。生产部门传达给采购和各级配套商时,又会层层“加码”。这样会增加供货商的成本,导致资金流更紧。
对汽车这种比较长的供应链而言,多层订单的冗余负担逐级放大,最终可能影响到整个生产链供应链的效率和成本,甚至伤害到产品本身,业内人士将这一痛点,称为“牛鞭效应”。
青山工业却给这一痛点开出了“药方”。
“药方”就在青山工业的电脑里。记者看到,在联网的企业资源计划系统上,清晰显示着销售和采购的准确信息,以及变化趋势。任何一个部件,在系统上下单以后,就会通过系统进行自动优化分配。
“这完全改变了供应链的信息传递方式。”青山工业采购配套部副部长叶虹麟介绍,汽车一些复杂零部件,可能会对应3级甚至4级供应商,而有的零部件又往往不只对应单独一个供应商,整个体系极其复杂。如果是传统的人工传达、干预和调整,不但效率低,稍有不慎还会因反馈不及时出现疏漏。
现在,通过信息化手段,不但能及时反馈梳理销售和采购的准确信息,还能智能研判变化趋势,实现与供应商的快速无缝对接。
“我们还建设了供应商与青山的协同管理系统。”叶虹麟称,如果有了关于新品开发的阶段性要求,每一个阶段需要供应商完成哪些工作,供应商上传确认,工作人员和供应商可以实时监控工作进度并分析风险和问题,100多个零部件的具体情况一目了然,每个供应商都能看到准确的供货时间点和量。任何项目方面的调整,比如延迟或者提前,也会通过这个系统第一时间发布,供应商可以随时掌握。整体效率比“人工时代”高出数倍。
信息化、智能化给青山供应链带来全方位变化。近日,该公司在自主创新方面取得重大成果,实现了DCT自动变速器上的核心部件——液压模块的自研自制。目前,首个基于自主技术的液压模块已下线,成功填补国内产业空白。
“该液压模块能够自制成功,不仅体现了我们技术水平的提升,更体现了供应链的整体进步。”采购配套部副部长王承斌表示,过去由于对供应链的整合能力不够,无法支撑这个模块的制造,而青山近年来通过信息化、智能化给供应链体系赋能,最终把这条供应链给打通了。
金康为何能造出全球首款续航“破千”新能源汽车?
重庆金康新能源汽车有限公司
成立于2012年,是国内最有代表性的新能源汽车企业和汽车科技公司,现有配套企业170家左右。
日前,重庆金康新能源汽车有限公司(以下简称“金康”)推出SF5自由远征版,该车搭载三合一电驱+智能增程系统,其NEDC(欧洲续航测试标准)综合续航里程可达1000公里以上,是全球首款NEDC综合续航“破千”的新能源汽车。
近年来,国内有不少汽车品牌提出将量产续航超过1000公里的新能源车型,但最终第一个实现的却是金康。分析个中原因,其搭载的全新驼峰智能增程系统功不可没。
该系统由金康和华为共同研发,实现了金康领先的三电技术和华为Drive ONE三合一电驱动系统整合。这也是全球第一套融合华为Drive ONE三合一电驱的智能増程/纯电动力系统。
除了“驼峰”,金康的“绝活”还有很多。例如,由其研发的首款基于自主封装碳化硅(SiC)器件的逆变器,近日成功通过电驱动系统联合测试,成为国内首家掌握该技术的企业。
研发,是金康的核心竞争力。早在2016年1月,金康就在美国硅谷成立研发中心,最多时有超过500名研发人员。金康还获得加州了自动驾驶牌照,并联合美国密歇根大学成立了智能驾驶研究中心。
近年来,该公司将更多研发资源投入国内,按照工业4.0标准打造了重庆两江智能工厂。目前,金康在新能源领域的全球专利已经超过1000多项。
近期,金康已在高寒、高温、高原等极端的测试条件下完成了产品的定向交付,而下一代的增程器、全新的电机和电控的核心技术也将进入量产阶段。
除了立足于自主研发,金康还在全球范围内进行了新能源核心技术的投资布局,成功投资了美国新能源三大领域的顶尖公司,包括固态电池、激光雷达和智能驾驶等。
如今,在新能源最核心的领域,无论是增程还是纯电,液态还是固态,同步电机还是异步电机,金康都走在了行业最前沿。
它给国内900多家车企当“医生”
重庆车辆检测研究院有限公司
2003年成立,属于国家级汽车检测机构,拥有汽车和摩托车两个国家级质检中心,获批筹建国家智能网联汽车质量检验中心(重庆),客户已覆盖国内900余家汽车、摩托车整车及零部件企业。
“幸好发现并整改了,不然车辆上市后有可能引发车祸……”3月11日,在重庆车辆检测研究院有限公司(以下简称“重庆车检院”),覃延明博士说起之前检测中发现的一个问题,如释重负。
前不久,作为国家级汽车检测机构,重庆车检院接到某品牌车企的一款新能源车整车测试订单。测试期间,负责汽车电磁兼容(EMC)测试的覃延明团队意外发现了一个漏洞——车辆电磁波干扰信号太强,检测结果偏离正常区间值太远。
“如果不整改,车辆在运行中可能会出现换挡、制动、雨刮器等失效的故障,严重影响行车安全。”针对此,覃延明团队及时排查干扰源,分析并提出整改方案。车企按方案整改后,产品再次测试通过验证。目前,该车已上市销售,赢得消费者喜爱。
实际上,作为一名“老测试工程师”,10多年来,覃延明遇到的类似案例数不胜数。仅检测电磁波干扰信号的电磁兼容实验室,每年至少都要测试200辆整车。
作为重庆汽车产业链的重要一环,重庆车检院目前已建立起整车、排放、动力、碰撞、部件汽车电子等多个实验室,拥有国内一流、国际先进的各种仪器设备约1750台(套),其客户包括国内900余家汽车、摩托车整车及零部件企业。