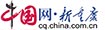
2020年3月20日,在位于重庆两江新区的长安汽车两江基地乘用车工厂焊接车间,机器人正在整车线上有序生产。记者张锦辉摄/视觉重庆
2019年10月24日,长安汽车两江基地乘用车工厂冲压车间,工人通过中控台监控封闭式高速智能冲压生产线。记者张锦辉摄/视觉重庆
2019年7月26日,渝北区仙桃数据谷,长安自动驾驶车驾驶台上方的传感器和摄像头。记者崔力摄/视觉重庆
1958年,木头汽车开上街。(重庆日报资料图片)
1993年3月10日,一辆红色长安牌微型汽车徐徐驶下生产线。至此,重庆长安机器厂已生产10万辆长安牌微型系列汽车。黄晓华摄
新中国第一辆吉普车与设计者之一路国玺。杨波摄
长安汽车渝北工厂总装车间,几百台机械臂不停舞动,生产线上的自动涂胶机器、自动装备器、图像精准定位仪等一起奏响“智慧”之音。
位于璧山区的重庆青山工业集团智能制造数字化工厂内,智能防错系统传感器逐个给变速器“体检”,这批产品将送往长安汽车,凡有丝毫瑕疵,均会被毫不留情地“逮到”。
位于南岸区的重庆机床集团车间,几位工程师给一台磨齿机增加振动和温度传感器,提升机床的智能补偿能力。而青山工业自动变速器齿轮生产线上,使用的就是同款智能磨齿机。
8月31日,3个“智慧”镜头串起一整条智能化产业链。从过去的“傻大粗”,到如今的“智细精”,以汽车产业为代表的重庆制造业,正在呈现全新的面貌和气象。
过去操作靠手上功夫现在有自动设备
8月31日,长安汽车冲压车间,2条5序“多连杆机械压机+双臂横杆传输方式”的封闭式高速冲压生产线,正按照每分钟10-15冲次的节拍工作,这是行业内少有的一条智能冲压生产线,车间压机全部由国内自主研制,仅需3分钟就可完成模具更换。
“要是过去的普通生产线,光换模就要好几十分钟。”一位现场负责人表示,智能化改造使得如今冲压设备效率提升了25%,质量、成本控制等方面的提升也是巨大的。
在总装车间轮胎安装区,工人正在操作一台自动拧紧螺丝的设备,该设备有5个孔轴,可同时拧紧一个轮胎上的5颗螺丝。
过去想要保证所有螺丝的扭力一致,主要靠工人的经验和感觉,一旦扭力出现较大差异,会明显影响轮毂的寿命和驾驶性能。而如今,通过设备上的扭力传感装置,出现扭力差异时,生产线将立即报警,进行差错修正,以保证轮胎螺栓连接安全可靠。
长安汽车敢于在生产线上大规模采用自动化,底气来自于各种汽车配件的标准化。
如为长安汽车配套的青山工业,新建了国内首个2万平方米密闭正压总装厂房,整线自动化率达到46.6%,远高于同行业DCT线29%的平均水平。
青山研究院院长王海兵表示,汽车变速器制造的精密程度,会影响到整台汽车的性能、驾乘体验和品质感。与过去相比,智能化程度的提高,大幅提升了青山DCT自动变速器的制造精度和一致性,同时,也让长安汽车的动力总成在同级别车型中领先。
青山工业能造出好的变速器,重庆机床集团功不可没。凭借重庆机床集团提供的智能磨齿机,青山工业能为变速器造出好齿轮。
近期,重庆机床集团又向青山工业交付了一批智能磨齿机。在机床操作面板上,只需要输入工件、刀具等具体参数,就能够自动生成齿轮加工程序。机床可以根据工艺数据库,智能推荐磨削加工方案,甚至可以根据磨削功率值变化,自动优化参数,进行补偿控制。
“过去操作机床,靠的是人的眼力、手上功夫,只有经验丰富的老师傅,才能熟练操作传统机床。”重庆机床集团副总工程师廖承渝表示,而如今,一台智能机床自身就相当于一个老师傅。在他看来,智能化正“悄悄”改变每个生产环节,重庆制造,正由“旧”转“新”。
过去企业研发自己搞现在上下游联合攻关
最近,长安汽车和青山工业联合谋划了一件“大事情”——联合攻关混合动力汽车智能驱动。
青山工业派出机械、液压、软件、电机工程师团队“驻扎”在长安汽车。在产品研发初期,团队共同完成产品策划、定义、论证,并在长安汽车现场进行产品设计。
而到了样机试制阶段、工程化开发阶段,长安汽车则派出相应的技术团队常驻青山工业,配合完成相应的研发、生产工作。
同时,双方办公系统及开发工具也实现一体化,可实现异地同步交流,图纸设计、评审等,进一步提高了工作效率。
“传统的制造行业,一般是主机厂提出产品要求,配套企业自己想办法达成。”青山工业负责人说。
而在新的协同创新模式下,青山工业在核心部件,以及长安汽车在动力总成匹配上的优势都得到充分发挥,项目开发进度可加快一倍。
同样的事情,发生在青山工业与重庆机床集团之间。
磨齿机涉及到齿轮修形,这是为了在齿轮工作受力变形的情况下,仍然能够实现一个比较好的接触面,从而提升变速箱齿轮噪音控制和稳定性。按照行业通常要求,修形后形状误差控制在六七个微米即可。而前段时间,青山向机床集团提出,变速箱齿轮的修形误差必须控制到2微米,相当于一根头发丝粗的四十分之一。
对此,机床集团携手青山工业、重庆大学和国外合作单位,对机床技术进行了大量智能化提升,完善程序功能,实现磨齿机参数智能调整,避免齿面烧伤……突破一个个难关,最终使误差达到2微米要求,也与国际同类先进产品处于同一水平。
依托智能化,机床集团也从过去单独提供机床,发展为提供成套的解决方案,除了青山工业以外,还帮助重庆蓝黛传动、万里扬、双环传动等国内一流企业建设智能化车间,驱动产业链由“旧”转“新”。
智能化改造“全面开花”已成为提级赋能主引擎
长安汽车、青山工业、重庆机床集团的故事,是重庆制造业大力推进智能化的示范和缩影。
市经信委有关负责人表示,智能化改造正在重庆制造业中“全面开花”。
位于两江新区的重庆金康赛力斯两江智能工厂内,1000多台机器人高效工作的场景,替代了传统生产线上的人头攒动,关键工序全部实现智能化生产,全过程只需几位技术人员通过屏幕进行操控;长安汽车冲压工序实施智能化改造后,生产效率提升了30%、能源利用率提升了11%。
在重庆綦江,有着90年历史的綦江齿轮传动有限责任公司一度经营困难,但通过引入6条自动化生产线,该公司在节约近90%人力的同时实现了产能倍增,年产变速器达到20万台;重庆荆江汽车半轴股份有限公司投资近2000万元引进智能化生产线后,生产效率提升了40%左右,产品质量也显著提升,去年还跻身美国通用、德国奔驰等全球知名企业的供应商……
据重庆市经信委统计,2019年重庆推动建设了1280个智能化改造项目、115个数字化车间和25个智能工厂,这些示范项目建成后生产效率平均提升了68.7%、产品不良品率平均降低了38.6%、运营成本平均降低了20.8%。
而截至今年7月底,我市狠抓企业智能化改造,累计完成改造2200个项目,建成数字智能工厂67家、数字化车间539家,智能化改造“全面开花”,带动企业生产效率大幅度提升,成为拉动工业技改投资的主动力和产业提级赋能的主引擎。
数读>>>
2200个
重庆狠抓企业智能化改造,截至2020年7月底,累计完成智能化改造项目2200个,建成数字智能工厂67家、数字化车间539家
68.7%
2019年重庆推动建设了1280个智能化改造项目、115个数字化车间和25个智能工厂,这些示范项目建成后生产效率平均提升了68.7%、产品不良品率平均降低了38.6%、运营成本平均降低了20.8%
5万家
重庆市已引进培育47个提供第三方服务的工业互联网平台,累计推动5万多家制造企业“上云上平台”。如今,重庆正成为国内工业互联网产业高地,国家工业互联网顶级公共标识解析节点的五个总部之一,也设在重庆
(数据由市经信委提供)
(陈钧、白麟)